With the advancement of various infrastructure constructions, the increasing of market demand for sand and gravel aggregates and the contradiction between supply and demand. Machine-made sand, as a natural substitute for natural sand, effectively fills the gap in market demand for sand and gravel. There may be some problems that affect the quality of machine-made sand in the actual production process. Vanguard Machinery will briefly introduce the factors affecting the quality of machine-made sand and how to improve it for your reference.
Sand making raw material control
1.Quality control of sand and gravel raw materials
(1).Rocks, ore, tailings
Before mining the raw material, it is necessary to remove the covering layer on the top of the material yard to ensure that there are no grassroots, covering soil, and other materials on the surface of the mining layer.
(2).Construction waste, concrete blocks, etc.
The construction waste can be pre-processed in advance, and after the debris is sorted out, the crushing equipment is used for crushing, and the iron products and steel bars in the construction waste are separated by the iron remover, so as to ensure the quality of the finished product.
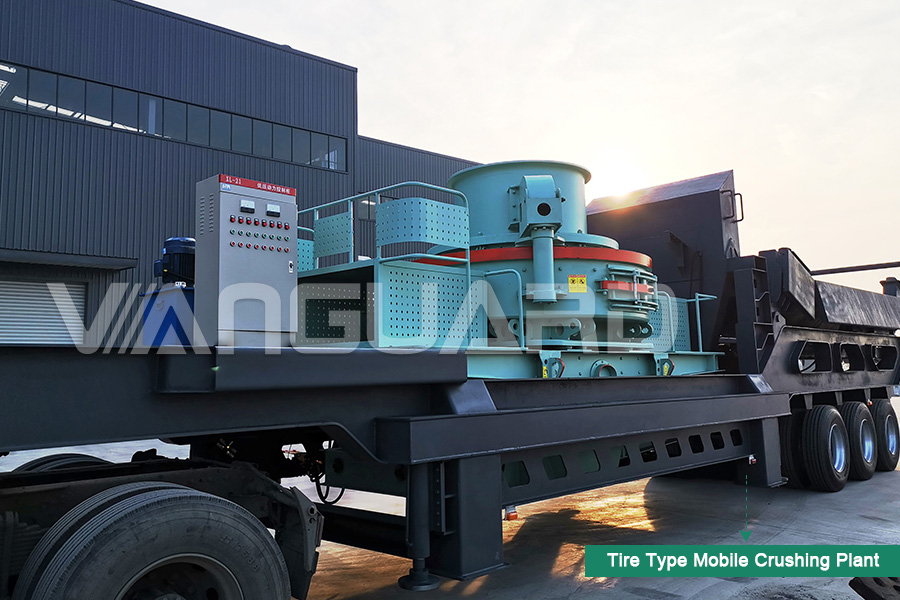
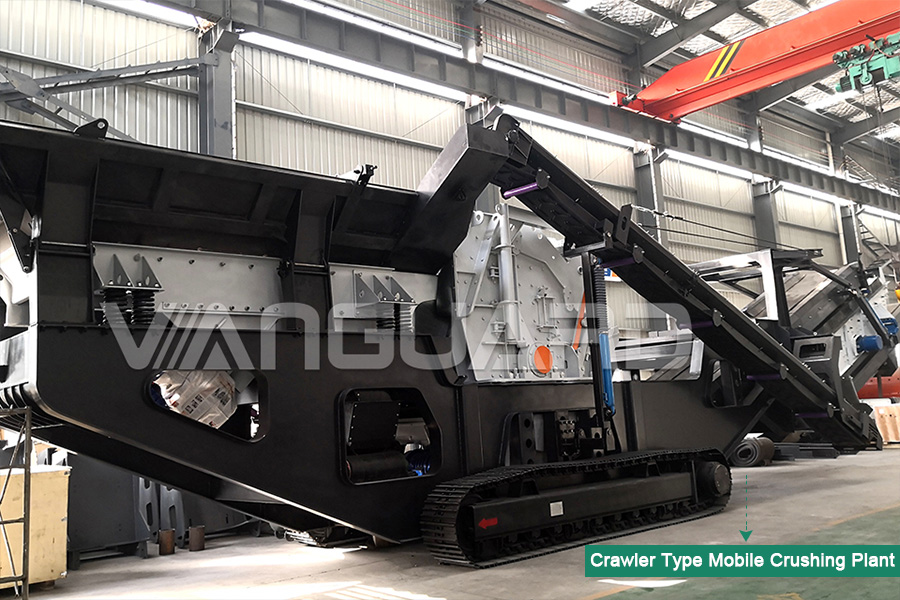
2.Control of the content of weak particles and mud content
The content of weak particles in concrete should not exceed 5%-15%.
(1).Before mining and processing, it should thoroughly clean the particles and sludge on the surface of the raw material and then strip clean to achieve effective control of the weak particles and sludge from the source.
(2).If there are mud or fine mud impurities in the raw material, it is necessary to use the screening workshop to remove the mud on a large scale.
(3).Usually during the production of sand and gravel aggregates, it is ensured that the water pressure and water consumption in the screening workshop and the sorting workshop are strictly controlled. According to the actual cleaning results of the sand and gravel aggregates, increasing water pressure and water consumption at any time, in favor of production of the mud content of the sand and gravel aggregates need to fully meet the standard specifications.
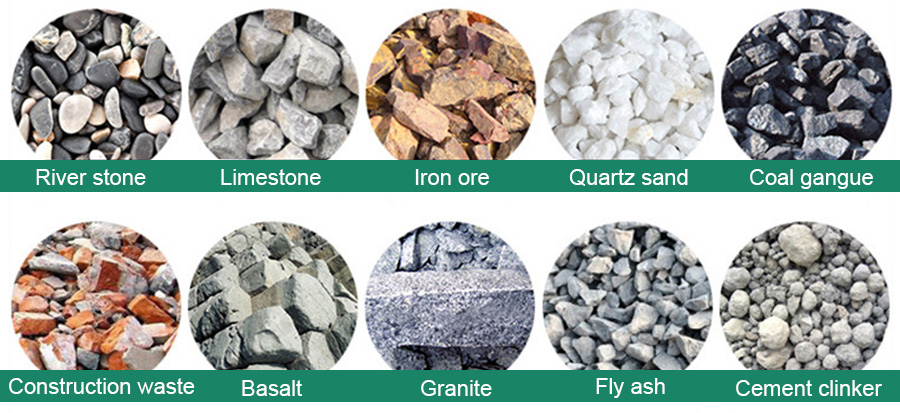
3. Control of needle flake content
It is mainly through the selection of equipment to control quality of the artificial coarse aggregate needle flake content. Secondly, the adjustment of the lumpiness of the feed in the production process.
Due to the different mineral composition and structure of various rocks, it also has different for the grain shape and gradation of the crushed rocks. There are many worst grain shape of needles and flakes in hard quartz sandstone and various immersed igneous rocks, while there are little needles and flakes in medium-hard limestone and dolomitic limestone.
Different crushers have different effects on producing needle flake content. The jaw crusher has a slightly higher content of needle flakes than the coarse aggregate produced by the cone crusher, while it is significantly reduced the needle flake content of the coarse aggregate produced by the impact crusher, especially the hammer crusher.
The content of needle flakes of coarse crushing is greater than that of medium crushing, and the content of needle flakes of medium crushing is greater than that of fine crushing. The larger the crushing ratio, the greater the content of pin flakes. In order to improve the shape of the aggregates, the production process should minimize the size before coarse crushing, and try to use coarse and medium crushed small stones and medium stones to make sand, and use finely crushed medium and small stones as the finished product of coarse aggregate. In this way, it can strictly controll the needle-like content.
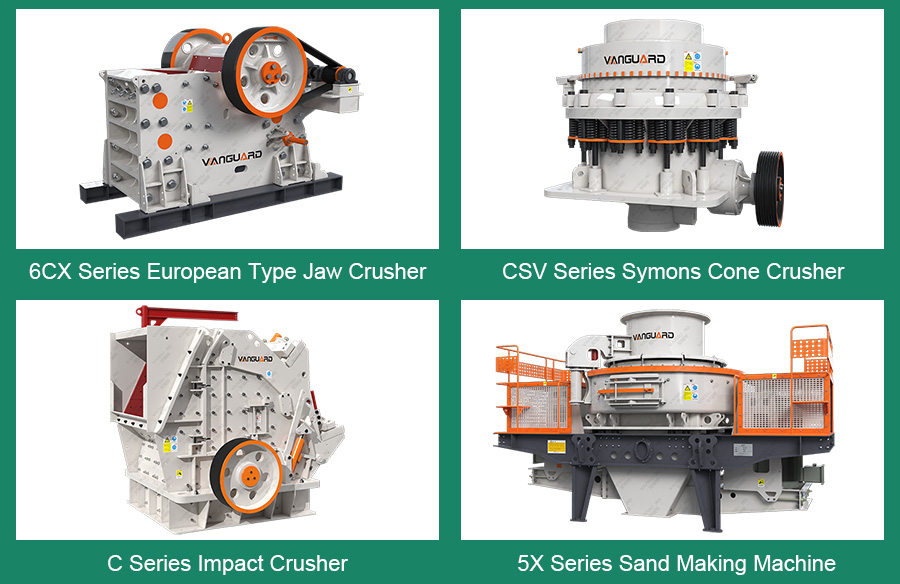
4.Control of stone powder content
The content of stone powder mainly refers to the content of particles less than 0.16mm in the aggregate, which can be regarded as an admixture. A reasonable content of stone powder can improve the workability of concrete and enhance the compactness of concrete.
The content of stone powder in the dry sand making process is generally high, and different screens can be replaced according to different needs to realize the control of the stone powder content.
It is generally low of the content of stone powder in the wet sand making process, and most of them require the recovery of part of the stone powder. Therefore, a stone powder recovery workshop (or fine sand recovery workshop) can be set up. In addition, the following measures can also be taken:
(1). Through a series of repeated experiments, appropriately increase or decrease the stone powder content.
(2) In hydropower projects, it is necessary to establish the wastewater treatment pool as close to the belt conveyor as possible to facilitate the normal operation of the belt conveyor and form a powder state after being dried by the filter press.
(3). Setting up a stone powder storage site at the construction site can not only accurately adjust the increase, but also effectively reduce the actual water content.
5.Control of fineness modulus
The fineness modulus is an index that characterizes the degree and type of natural sand particle size. The larger the fineness modulus, the coarser the sand. Sand is divided into three specifications of coarse, medium and fine according to the fineness modulus, and the fineness modulus is respectively: coarse is 3.7~3.1; Medium is 3.0~2.3; Fine is 2.2~1.6. The fineness modulus of the finished sand can be reduced by reducing the feeding amount and particle size of the feeding hopper, or the content of the grading particles can be increased to adjust the gradation of the finished sand.
6. Control of water content
Based on the current situation of sand and gravel aggregate production in hydropower projects, in order to control the moisture content within a reasonable standard range, most engineering projects use mechanical dehydration methods, and a very small number of projects use natural dehydration methods. Details as follows:
In the production process of sand and gravel aggregates in hydropower projects, the vibration dehydration process is widely used, which can reduce the original water content from more than 20% to about 15%. A few projects also use vacuum dehydration and centrifugal dehydration, and the dehydration effect is better, but Larger investment.
Artificial sand and gravel reclaiming and storage dehydration are generally carried out separately. Generally, it is in a stable state when the water content can be reduced to less than 6% after 3-5 days of storage and dehydration. It can also have the effect of reducing the moisture content by mixing dry artificial sand into the finished sand silo.
Rainproof sheds can be constructed at the top of the finished sand silo, and drainage and concrete floor infrastructure can be added at the bottom. The drainage channels are regularly cleaned to avoid blockages and minimize the water content of sand and gravel aggregates.
Machine-made sand production equipment and process method control
Therefore, it has a direct relationship with product quality for the selection of machine-made sand equipment and the process method. For example, a heavy-duty hammer crusher is more targeted for limestone crushing, which final product is excellent grain shape and reasonable gradation. According to the feeding method of the material, the feeding method of the 5X new type sand making machine can be divided into fully central feeding and central feeding with circular cascade feeding. According to the compressive strength and abrasiveness of the material, the crushing method of the sand making machine can be divided into crushing between stone and rock and crushing between stone and plate, which are used for shaping and sand making. Therefore, when selecting equipment, users can choose according to their own processing materials, feeding methods, processing volume, feed size, finished size, and actual requirements. Let Vanguard Machinery's engineers select a reasonable selection for you to conduct coarse crushing, medium crushing, fine crushing and other operations to improve effectively the quality of machine-made sand products.
Human factors control
Operators’ own professional technical skills and quality awareness are important factors that affect the quality of sand and gravel. Therefore, relevant personnel need to improve their professional and related skills, master the production process of machine-made sand, and respond to special situations such as fault maintenance. So as to produce good quality machine-made sand.
In summary, the quality of machine-made sand closely relate to many aspects. It must not only consider the raw materials for sand making but also the reasonable configuration of machine-made sand production equipment and process methods, as well as the professional level of the operators. It should continues to increase production quality control, effectively improve the quality of machine-made sand to ensure the overall quality of the project.