Ball mill is the key equipment for crushing materials after being crushed, which is suitable for cement, silicate products, new building materials, refractory materials, fertilizers, non-ferrous metal beneficiation, glass ceramics, and other industries, and applied to dry or wet grind all kinds of ores and other grindable materials. So, how do choose between dry grinding and wet grinding when choosing a ball mill to grind materials? Let's analyze it from the following aspects:
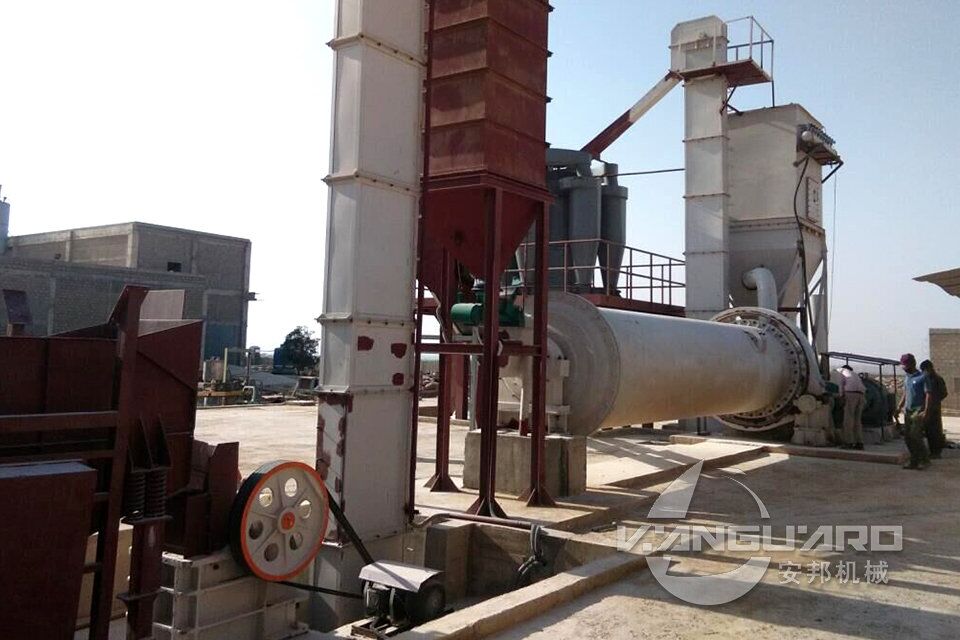
What is dry and wet grinding?
Dry grinding
Dry grinding refers to that the ore has a certain crushing operation in the ball mill, and it will be discharged by the airflow drawn out of the cylinder when it meets the requirements. The dry ball mill is used in the dry grinding process. It does not need to add water during the production process, and the material must be dry, so it is called a dry mill. The equipment is straight cylindrical equipped with an air induction device, a dust exhaust pipe, and a dust collector. It plays an important role in grinding in the production of various minerals.
Wet grinding
Wet grinding means that after the ore enters the mill, it will complete an amount of ground under the interaction of the grinding medium and the ore itself to meet the grinding needs of the user. At the same time, the movement of the ore needs to be driven by water flow that adds to the process. The ball mill used in the wet grinding process is a wet ball mill. According to the motion characteristics, it can be divided into three types: simple swing type wet ball mill, complex swing type wet ball mill and mixed swing type wet ball mill.
What is the difference between dry grinding and wet grinding?
1. Structure of ball mill
The basic structure of both is composed of the main parts such as the feeding part, the discharging part, the rotating part, and the transmission part (reducer, small transmission gear, motor, electric control).
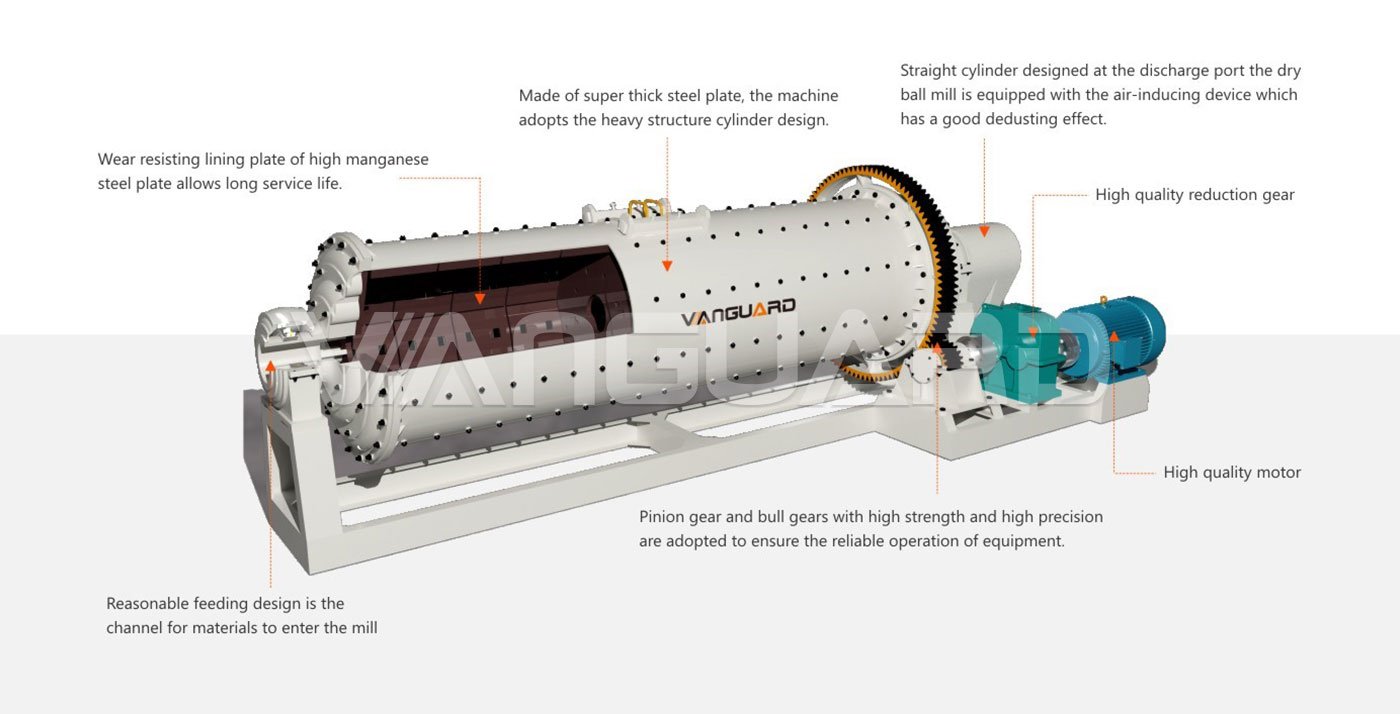
The difference between the two structures is that the discharge port of the dry ball mill is straight cylindrical, and it is also equipped with an air-inducing device to discharge dust. The discharge port of the wet ball mill is trumpet-shaped and has a built-in screw device for easy discharge. Most of the wet ball mills sold in the market have high grinding fineness and good beneficiation effect.
2. Working principle
The dry ball mill is a cylindrical rotating device that driven by an outer gear with two bins and a grid type ball mill. The material enters the first bin of the mill spirally and evenly through the feeding hollow shaft from the feeding device. There is a step liner or a corrugated liner inside the bin, which contains steel balls of different specifications. The rotation of the cylinder generates centrifugal force to bring the steel balls to a certain height, and after falling, it will have a heavy blow and grinding effect on the material. After the material reaches the rough grinding in the first warehouse, it enters the second warehouse through the single-layer partition board. The warehouse is lined with flat liners and steel balls to further grind the materials. The powder is discharged through the unloading grate to complete the grinding operation.
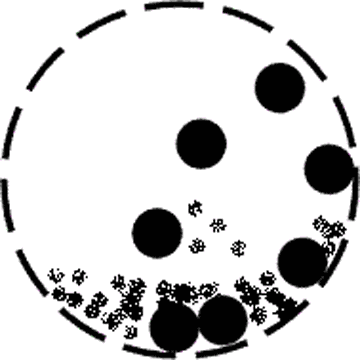
The working principle of the wet ball mill is basically the same as that of the dry grinding method, that is, the liquid medium needs to be added in the grinding process, and attention must be paid to the proper control of the grinding concentration. The amount of water added is generally determined by the use of the mud, the amount of clay in the formulation, and the water absorption value of the clay. The material is gradually crushed under the action of impact and grinding. The crushed ore is discharged out of the barrel through the discharge part. After the discharged minerals are classified into qualified products in the spiral classifier, the coarse sand passes through the combined feeder and returns to the ball mill to continue grinding. The feeder feeds continuously and evenly, the ore enters the ball mill continuously and uniformly through the combined feeder, and the ground materials are continuously discharged from the ball mill.
3. Applicable conditions
During dry grinding, due to the design of the barrel, sometimes dead corners are formed, and some materials in the dead corners cannot be ball milled. However, wet grinding also has a weakness compared with dry grinding, that is, the powder after wet grinding needs to be dried to remove moisture or other liquid media, which will increase energy consumption and cost; Wet grinding cannot be used for cement. Therefore, the two have their own characteristics, and the appropriate grinding method should be selected according to the needs when the material is ground.
4. Their respective advantages
Advantages of dry ball mill:
(1) Dry ball mill adopts grate plate type grinding tail discharging with smooth discharging, there is no phenomenon of rising and grinding, the cylinder does not need to be cooled with long service life and low failure rate.
(2) There are many auxiliary equipment of dry ball mill. The original structure of the mill is changed to integrate the machine body and the chassis that can be hoisted on the foundation plane at one time during installation. The main shaft adopts double-row radial spherical roller bearings, that can reduce energy consumption by 30%.
Advantages of wet ball mill:
(1) The wet ball mill has better performance and higher grinding efficiency. It has low requirements for ore water content and can process ores with high water content and mud content.
(2) The wet ball mill has less auxiliary equipment and simple material transportation device, so the investment is about 5%-10% lower than that of the dry ball mill.
(3) Wet ball milling can not only grind the agglomerates into fine particles (but rarely split particles)-round particles, but also force barren materials and plastic materials to mix evenly.
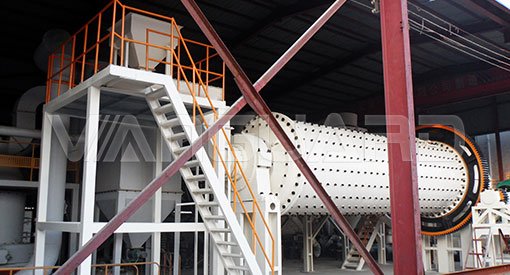
How to choose dry and wet ball mill
1. Correctly choose the feeding way of dry grinding and wet grinding
Whether feed the material dry or wet depends entirely on the subsequent operations in the ball mill and the nature of the produc Some materials require dry grinding because they will undergo physical or chemical changes after adding water. In addition, during the fine grinding process of the material in the ball mill, the dry grinding on the liner and the medium is relatively small, to the opposite, the proportion of the fine particle level in the product is relatively large. This may be what people need the grinding method in some cases. Only by finding the suitable grinding method of the material can be able to ensure the quality and efficient operation of the ball mill. The two types of ball mills have their own advantages, and the dry and wet grinding feeding methods should be correctly selected according to the specific situation.
2. Wet grinding is economical and more commonly used than dry grinding
Considering the overall economic effect of the ball mill grinding operation, wet grinding is generally used in beneficiation. The wet ball mill is also the most widely used because of its strong adaptability to materials, continuous production, large crushing ratio, and easy speed adjustment to grind the fineness of the product. The discharge port of the wet ball mill is trumpet-shaped and has a built-in screw device for easy discharge. Most of the ball mills sold on the market are wet ball mills with high grinding fineness and a good beneficiation effect.
3. Matters needing attention in the process of choosing dry and wet grinding
1) When the particle size of the powder is not required to be very fine, or when the ball-milled product needs to be stored or sold in powder form (such as the grinding of glazes and pigments), and when products such as tiles are pressed, the dry grinding process is used Is appropriate. For example, in the production of cement, dry grinding must be selected instead of wet grinding, otherwise it will be difficult to meet the needs.
2) For dry milling, it is generally for materials that do not react in the liquid medium. If there is a reaction, there is meaningless ball milling, for other substances will be formed in the ball mill.
3) During the dry grinding of the ball mill, forming dead corners sometimes that some materials are not ground in the dead corners by balls due to the design of the ball mill tank, that is something we need to pay special attention to in our daily operations.